Le prime congiunzioni potevano avere disegni elaborati; certamente nelle biciclette da corsa inglesi e italiane le forme finemente decorate mettevano in evidenza la maestria del costruttore. Gli artigiani trasformavano, con il lavoro manuale, congiunzioni grezze in vere e proprie opere d’arte anche se l’estetica aveva spesso poco a che fare con i principi veri e propri della costruzione di qualità. Anche produttori francesi come Oscar Egg e Nervex, realizzarono nelle loro fabbriche congiunzioni con complessi intagli di alleggerimento. Nei cataloghi ogni forma corrispondeva ad un numero di serie e potevano essere realizzate anche solo su ordinazione, a volte il design veniva modificato e al codice veniva aggiunto un numero, poi modificato di nuovo e così via. Diverse le aziende in italia e all’estero dedicate alla produzione di congiunzioni, tra le più importanti Cinelli, Bozzi, Agrati, Rastagno, Prugnat, Roto, Hoto, Bocama, Nervex e Haden.
A partire dalla fine dell’800 il processo di produzione delle congiunzioni evolse adottando tecniche diverse. In questo articolo si descrive sinteticamente, e in ordine cronologico, le 3 tecniche più diffuse: pressatura, colata in sabbia e microfusione.
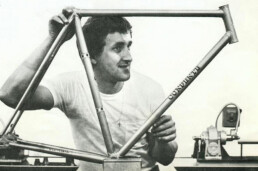
Fonti: Velofilie / Classiclightweights / Flickr Rusty753 / Classic Rendezvous
PRODUZIONE CON PRESSATURA A TAGLIO E SALDATURAfine '800 > anni '80
Un telaio di bicicletta classico è un insieme di undici tubi di acciaio tenuti insieme da congiunzioni saldate. Già a nell’800 la forma del telaio della bici era, come oggi, una cornice a forma di rombo con angoli di circa 70°. A fine ‘800 il processo per la fabbricazione delle congiunzioni era la saldatura: un pezzo di acciaio incandescente veniva martellato in uno stampo (spesso da mazze azionate a vapore) fino a divenire della forma voluta. Il risultato grezzo veniva poi lavorato con torni e fresatrici. Questo processo, l’unico in utilizzo fino al 1920 circa, comportava molto lavoro ed era costoso. Si realizzavano con questa tecnica sia congiunzioni per brasatura interna (congiunzione nel tubo) che per brasatura esterna (tubo nella congiunzione). Come nella bottega di un fabbro, la brasatura avveniva spesso in un focolare.
Processo di produzione mediante pressatura e saldatura / Catalogo Bridgestone
Tubazioni in acciaio Bozzi, 1956
Congiunzioni Emilio Bozzi prodotte con pressatura e saldatura.
Sopra grezze, sotto dopo la lavorazione di alleggerimento. / Via Fietssite
Congiunzioni in acciaio e ghisa pressata / Catalogo Donniselli
Nel 1949 la ditta Malaguti di San Lazzaro di Savena (Bologna) brevettò in Italia il metodo di pressatura senza taglio e saldatura, ottenute direttamente da tubi in acciaio tramite estrazione. Queste congiunzioni, più resistenti e facili da lavorare, ebbero da subito grande diffusione sul mercato e furono adottate da molti importanti costruttori di biciclette sportive tra i quali Frejus, Legnano e Cinelli che le utilizzò su tutti i telai Super Corsa fino ai primi anni ’60.
Processo di produzione mediante estrusione di foglio d’acciaio / Foto Flickr Rusty753
Dall’alto a sinistra: immagini 1, 2 e 3 una piastra di acciaio viene pressata in due fasi in una forma di cartuccia. Nell’immagine 4 il lato chiuso è stato tagliato e quattro bulbi vengono pressati dall’interno; nell’Imm. 5 i bulbi sono stati tagliati e vengono tirati dall’interno verso l’esterno.
Congiuzioni pressate RGF e Bocama realizzate con la tecnica dell’estrusione senza taglio. / Via Fietssite
Cinelli Supercorsa del 1957 con congiunzioni prodotte con la tecnica ad estrusione Malaguti / Foto Frameteller
Esempi di congiunzioni stampate grezze e non tagliate (probabilmente prodotte dalla Agrati Milano) erano distribuite in Italia e all’estero dall’azienda di Emilio Bozzi di Milano, proprietario di Wolsit, Frejus e Legnano, marchi molto rinomati già dopo la prima della guerra mondiale. Wolsit scomparve negli anni ’60, ma Frejus e Legnano rimasero competitive sul mercato fino agli anni ’70.
Fino alla fine degli anni ’50, e in alcuni casi anche nei decenni successivi, la pressatura fu la tecnica preferita alle tecniche di fusione perché, oltre ad essere più economica, consente di creare congiunzioni modellabili a seconda delle esigenze del costruttore e adattarsi meglio alle tubazioni in acciaio, sempre più sottili.
Congiunzioni pressate Bozzi, probabilmente costruite da Agrati Milano. Catalogo Emilio Bozzi fine anni ’40
Congiunzioni AGRATI Milano
ll kit di congiunzioni in acciaio pressato Nervex Professional è oggi universalmente considerato un classico dell’epoca. Fu notevolmente prolifico negli anni ’50 e ’60, quando erano scelte da quasi tutti i produttori di telai, dai migliori artigiani Gillott, Bates, Ephgrave, Jack Taylor, De Rosa, Colnago, Bianchi, Masi e dalla maggior parte dei produttori di media e grande distribuzione come come Viking, Dawes, Holdsworth, Carlton, Mercian, Raleigh, Peugeot e Schwinn, Paramount negli Stati Uniti.
Fino all’avvento alla fine degli anni ’40 della serie di congiunzioni già intagliate Nervex Professional, molti costruttori le dovevano alleggerirle internamente con aggravio di energie, tempo e denaro. Progettate con un design elegante, erano destinate ad avere un grande successo fin dal giorno in cui entrarono sul mercato. Splendidamente tagliate con linee piacevoli, relativamente leggere e ben rifinite, richiedevano meno limatura e pulizia rispetto ai modelli fusi “a colata di sabbia” disponibili all’epoca. Parte della loro popolarità globale dipese anche dal fatto che erano usate nelle biciclette scelte da importanti corridori professionisti.
Ovviamente i migliori costruttori continuarono a rendere riconoscibili i propri telai anche attraverso un intaglio unico ed originale di queste congiunzioni.
Congiunzione Nervex / Foto Flickr Rusty753
Al centro una congiunzione Nervex Professionel dei primi anni Cinquanta; dal 1956 le due piccole corna vengono sostituite da una coda di pesce come si vede a sinistra. La congiunzione a destra era venduta da Bozzi, è una forma grezza, di qualità inferiore a quella della Nervex. / Via Fietssite
Nodo sella Nervex con un design simile a quello ideato da Faliero Masi per firmare le proprie bici.
Congiunzioni Nervex Professional
Nervex”serie legere”, molto diffuse ma meno rifinite e decisamente meno costose delle Professional / Catalogo Nervex 1958,
Congiunzioni pressate Cinelli anni ’60/’70.
PRODUZIONE “COLATA IN SABBIA”
primi ‘900 > primi anni ’70
A inizio ‘900, con il miglioramento dei processi nelle fonderie, si diffuse velocemente una nuova tecnica chiamata “colata in sabbia” che convisse per decenni a fianco della pressatura.
In quegli anni la maggior parte delle biciclette erano utilizzate principalmente per il trasporto di persone e materiale e questo metodo di fabbricazione consentiva di ottenere prodotti decisamente più robusti e di lunga durata.
Il lavoro con questa tecnica era più semplice ma più costosa rispetto alla pressatura e le congiunzioni erano ancora troppo pesanti e non adatte alla costruzione di bici per uso sportivo, dove la leggerezza era sempre più importante, inoltre essendo troppo rigide potevano verificarsi delle crepe nell’adattarsi alle nuove tubazioni in acciaio sempre più sottili.
La colata in sabbia venne impiegata per la costruzione di bici sportive solo verso la fine degli anni ’50 e fino a metà anni ’70, in particolare per scatole del movimento centrale e teste forcella. Aziende come Georg Fisher, EKLA produssero congiunzioni a colata di sabbia di grande qualità, fresate per assottigliarne lo spessore e poter aderire meglio alle tubazioni.
Processo di produzione “colata in sabbia” / Catalogo Bridgestone
Stampi per congiunzioni Georg Fisher
Scatola movimento centrale prodotta da Georg Fischer nel 1973, realizzata con colata in sabbia prima e dopo il lavoro di rifinitura.
A sinistra la forma grezza, a destra la forma rifinita a mano.
Teste forcella e scatola movimento George Fisher
1950 Hobbs of Barbican, congiunzioni Ekla alleggerite / Foto Classic Lightweights UK – Hilary Stone
Congiunzioni piuttosto popolari nel mondo anglosassone tra gli anni ’40 e 50.
Legnano Gran Premio 1958, congiunzioni a colata in sabbia Emilio Bozzi / Foto My travels note
Scatola movimento centrale prodotta con colata in sabbia / Foto Flickr Rusty753
Scatola movimento centrale De Rosa grezza, prodotta con colata in sabbia / Foto Flickr Rusty753
PRODUZIONE IN MICROFUSIONE O “A CERA PERSA”
primi anni ’70 >
Alla fine degli anni ’60 il costruttore artigiano Licinio Marastoni di Reggio Emilia, fu il primo a pensare di impiegare la tecnica (già esistente) della microfusione o “fusione a cera persa” per produrre congiunzioni e teste forcella delle biciclette di uso quotidiano e sportive. Nel 1971, su insistenza di Cino Cinelli, Marastoni investì nella commissione, all’azienda MFI Micro-Fusione Italia, di una intera serie di congiunzioni da testare. Oltre a Cinelli, l’esperimento attirò da subito l’attenzione anche quella di altri maestri come Masi, DeRosa e Colnago i quali a più riprese visitarono l’officina per osservare la nuova invenzione. Le parti realizzate con questo processo erano costose, ma la sagomatura erano più precisa consentendo di risparmiare molto tempo durante la costruzione del telaio. A partire dal 1973 anche altre aziende, come la ROTO di Bologna, produssero congiunzioni con questo metodo e negli anni ’80 si affermò come lo standard in tutto il mondo. La maggior parte dei marchi, anche Cinelli e Colnago, esternalizzavano la produzione a ditte specializzate come la MFI.
Processo di produzione a microfusione o “a cera persa” / Catalogo Bridgestone
Congiunzioni Marastoni prodotte con la microfusione o “a cera persa” dalla FMI.
Catalogo MFI anni ’70
Congiunzioni Colnago e Eddy Merckx prodotte con la microfusione o “a cera persa” / Foto Flickr Rusty753
Kit congiunzioni in microfusione Columbus SL primi anni ’80.
Negli anni ’70 le congiunzioni in microfusione come quelle di Cinelli avevano bordi affilati e la sovrapposizione per la brasatura era sottile. Le congiunzioni in lamiera d’acciaio stampate e saldate potevano essere facilmente deformate fino a 3 o 4 gradi, mentre per le congiunzioni fuse era possibile lo spostamento di un solo grado. La maestria del costruttore di telai consisteva in gran parte nella capacità di adattare perfettamente le congiunzioni rispetto agli angoli prefissati.
In quegli anni il maestro costruttore veronese Mario Confente, che da giovanissimo aveva studiato presso un’Istituto professionale la fusione e la lavorazione dei metalli, non era soddisfatto della qualità, estetica e funzionale, delle congiunzioni prodotte con la tecnica microfusione, le quali a suo giudizio erano troppo pesanti e facili a deformazioni tali da richiedere poi ore di lavoro manuale per essere corrette. Nei disegni delle sue congiunzioni, che inutilmente provò a brevettare, il problema delle inevitabile deformazione durante la solidificazione del metallo veniva evitato anticipandolo già nella forma dello stampo. Purtroppo pochi anni dopo, durante la sua avventura negli USA, l’imprenditore Bill Recht gli rubò di fatto idee, brevetto e progetto, qui potete trovare il racconto del suo ex socio Jim Cunningham.
Mario Confente. Catalogo Confente USA 1979.
Workshop Mario Confente, 3238 Union Pacific Avenue, Los Angeles, California USA / Foto Classic Rendezvous
Mario Confente insieme a Bill Recht (sinistra) / Foto Classic Rendezvous
Scatola e forcellino Confente alleggeriti. Telaio costruito nel 1973 a Verona.
Scatola movimento centrale alleggerita con il simbolo Confente. Catalogo Confente USA 1979.
Congiunzione sterzo alleggerita con il simbolo Confente. Catalogo Confente USA 1979.
Congiunzioni Confente USA anni ’70
Mario Confente USA, telaio N.1 / Foto Classic Rendezvous
La storia della costruzione dei telai è strettamente legata a diametro e dimensioni di tubi e filettature. Dagli anni Cinquanta agli anni Ottanta Reynolds e Columbus furono i leader del mercato. I francesi si attennero ai propri standard metrici per decenni. Le dimensioni inglesi sono espresse in pollici (1 pollice = 25,4 mm). Le filettature inglesi sono espresse in TPI, lo standard italiano è un misto metrico-imperiale e le filettature possono combaciare con quelle inglese ma non con quelle francesi. Durante l’ascesa della moda All Terrain Bike negli anni ottanta, la saldatura TIG divenne il metodo di costruzione più popolare e i costruttori di tubazioni adattarono la loro produzione per migliorare la saldabilità; forma e grippaggio divennero meno importanti per la saldatura. Anche i tubi oversize e aerodinamici furono molto apprezzati ma in realtà il mercato stava già imboccando la strada del carbonio.
Congiunzioni arabescate Colnago Arabesque, disegnate da Raul Gozzi (Rauler)
Congiunzioni Rauler, pantografate a mano. (Raul e Reclus Gozzi)
Forcellini Campagnolo, catalogo 1953/55
Forcellini Campagnolo per cambio corsa e paris-roubaix, catalogo 1955
Forcellini Campagnolo, catalogo 1955
Forcellini Campagnolo, catalogo 1967/68
Forcellini Campagnolo, catalogo 1973
Forcellini Campagnolo, catalogo 1975
1982-forcellini-campagnolo-droputs
1984-forcellini-campagnolo-droputs
Congiunzioni Cinelli per tubi oversize
Stelbel strada 1978, Stelio Belletti fu uno dei primi al mondo
a costruire telai senza congiunzioni con la tecnica a TIG.
SCATOLE MOVIMENTO CENTRALE
Le scatole economiche realizzate con fogli di acciaio pressati e saldati, non si adattavano sempre al meglio, mentre quelle realizzate per colata di sabbia degli anni Sessanta erano più robuste ma anche molto più costose e spesso con superfici piuttosto grezze che richiedevano un impegnativo lavoro di rifinitura. Nei primi anni Settanta fecero comparsa nel mercato le moderne scatole prodotte con la tecnica “a cera persa”, impiegate soprattutto nelle bici sportive di alta gamma. Le scatole del movimento centrale erano, e lo sono ancora, disponibili con filettatura inglese, italiana e francese. La larghezza era, a parte rare eccezioni come in certe Raleigh, Humber o Cinelli Super Corsa degli anni ’50, di 68 mm francese o inglese e 70 mm italiana. Le scatole francesi e italiane avevano la filettatura in senso orario su entrambi i lati: italiana 36 mm x 24 TPI e francese 35 mm x 1. Le dimensioni dei tubi per le staffe francesi erano metriche (28 mm) mentre inglesi e italiane usavano dimensioni imperiali (28,6mm). Di tanto in tanto si possono trovare scatole con misure francesi dove il lato guida era con una filettatura sinistra M35x1 (detta anche scatola svizzera).
La calotta lato trasmissione (destra) era fissa e i cuscinetti venivano regolati con la calotta sinistra. Le scatole inglesi avevano sempre una filettatura mancina sul lato guida 1.370 “x 24 TPI.
Scatola movimento centrale italiana prodotta dalla Bozzi negli anni ’50 / / Foto Flickr Rusty753
Scatola movimento grezza prodotta con colata in sabbia, anni ’50/60. / Foto Flickr Rusty753
Scatole movimento prodotte in microfusione Cinelli e Roto personalizzate con marchio Gazelle
Dal 1978 la Columbus acquistò la Cinelli, in quella occasione venne sostituito il leggendario fregio con il marchio disegnato da grafico milanese Italo Lupi. In quegli anni la Cinelli/Columbus produsse due tipi di scatole: SCM e CCM; la differenza era l’orientamento della brasatura delle forcelle posteriori.
La moda delle guide per i cavi del cambio cambiò alla fine degli anni settanta, quando da sopra passarono sotto alla scatola del movimento centrale. La scatola CCM aveva un piccolo foro per il montaggio dei passacavi in plastica, basso attrito, nessun danno alla vernice. Per un alcuni anni furono utilizzate anche parti saldobrasate in acciaio seguite da quelle già integrate nelle scatole in microfusione. La scatola “Spoiler“, sempre della Cinelli, fu un interessante pezzo di ingegneria ma era costosa, pesante, poco pratica e i cavi danneggiano comunque la vernice.
I passacavi in plastica rimasero comunque popolari e tornarono in uso in seguito .
Cataloghi Cinelli fine anni ’70/primi ’80. / Archivio Frameteller
Scatola alleggerita, Masi Special anni ’60, i passacavi passavano sopra.
Anni ’70, scatola movimento centrale Georg Fischer con passacavi saldobrasati, foto Frameteller.
Anni ’80, scatola movimento centrale con passacavi saldobrasati
Anni ’80, scatola Cinelli “Spoiler, i passacavi sono integrati nella microfusione.
un anello di battuta all’interno interno facilitava il posizionamento dei tubi.
FORCELLE
La maggior parte delle teste forcelle avevano piccoli bordi di 2mm o tasche, più o meno profonde (anche 14mm), per ospitare rinforzi e irrigidire l’insieme.
La linea delle teste forcella passo dalla forma piatta alla forma inclinata. Già negli anni ’50 costruttori come Marastoni e Cinelli usavano teste dalla forma inclinata per aumentare la rigidità della forcella.
La forcella è una parte interessante e complessa della bicicletta poiché è il principale contributo alla guidabilità della biciclettà. È composta da forcellini, foderi, rinforzi, tubo sterzo e testa. La sua forma può aumentare o diminuire la reattività, il comfort e la sicurezza della bici. La maggior parte dei costruttori di qualità utilizzava forcellini Campagnolo, tuttavia, ce ne furono molti altri (Gipiemme, Roto, Shimano Dura-Ace, Sun Tour, Simplex, Huret) di qualità soddisfacente. I foderi e il piantone dello sterzo erano prodotti dai principali produttori di tubazioni come Columbus e Reynolds.
Erano praticate tre tipologie di costruzione per le teste delle forcelle: pressatura, saldatura e fusione. Le corone pressate erano le più fragili e si trovano solitamente su biciclette di produzione poco costose, sebbene ci siano alcuni costruttori di telai che preferivano questa tecnica. In generale, i costruttori di telai di qualità sceglievano saldatura o fusione a seconda del tipo di bicicletta. Le teste saldate erano molto resistenti ma richiedevano un importante lavoro limatura. Come i foderi, la corona fusa era estremamente costosa ma molto resistente e in genere veniva fornita con il massimo grado di precisione nelle tolleranze. Esistono tre modelli di base di testa forcella: semi-inclinata, completamente inclinata e piatta, ognuno con vantaggi e svantaggi.
Teste forcella con bordi per ospitare i rinforzi, a sinistra il bordo è profondo 14mm, a destra 2mm.
Diversi design di testa forcella, per foderi tondi e ovali. La testa a sinistra si inseriva all’interno dei foderi.
Testa forcella Cinelli a doppia corona, si tratta in questo caso di tre diverse parti lavorate e assemblate, i rinforzi formano parte integrante della struttura).
Teste forcella con spalla piatta, semi-inclinata e inclinata.
Differenti teste per forcelle da 22mm. Dall’alto Cinelli, Bocama, Prugnat, Georg Fischer (colata di sabbia) Davis Components.
Nel dopoguerra, al ritiro dalle corse ciclistiche, Cino Cinelli iniziò a progettare biciclette e componenti per bici. Il modello di punta era il Super Corsa che utilizzava una forcella integrale in colata di sabbia saldata internamente. Si trattava di un pezzo d’acciaio piuttosto pesante. Cinelli credeva che le forcelle Reynolds standard non fossero sufficientemente rigide lateralmente; trovò quindi un fornitore italiano nell’azienda Columbus per costruire le sue biciclette con foderi 27,5x20mm e tubazioni telaio Reynolds. Iniziò così la collaborazione tra Cinelli e Columbus per la produzione e distribuzione mondiale di una linea completa di tubazioni per biciclette.
Cinelli progettò nuove parti di brasatura, non solo per le proprie biciclette, ma anche per la fornitura ad altri produttori. Gran parte del lavoro di fonderia era affidato a Georg Fischer in Svizzera ma anche ad altri produttori italiani, come la Agrati di Milano, che avevano un costo nettamente inferiore.
Cinelli Supercorsa 1957 / Foto frameteller
Testa forcella Cinelli a brasatura interna, prodotta dall’azienda svizzera Georg Fischer.
I foderi entravano all’interno della forcella creando un insieme unico.
Forcella anteriore a testa piatta per pista con foderi rinforzati. Foto Cinelli Only
Come detto precedentemente, nei primi anni Settanta Cinelli fu il primo, su idea di Licinio Marastoni, ad iniziare la progettazione e produzione di congiunzioni microfuse. La sua testa forcella semi-inclinata MR è realizzata per tubi Reynolds e la MC per le forcelle Columbus con profonde tasche per i foderi. La MC era invece un poco più larga e non necessitava di foderi. Reynolds iniziò a commercializzare una nuova forcella negli anni settanta in una misura quasi identica alla Columbus (Continental New Oval) per poter utilizzare le nuove teste forcella SC e CC. Le congiunzioni in microfusione si adattavano molto bene ai tubi richiedendo meno lavoro per la costruzione del telaio. All’inizio degli anni Ottanta la moda aerodinamica, di cui Cinelli fu uno dei primi autori, lo portò a ridisegnare le sue corone SC e CC; SCA e CCA erano più leggere e più aerodinamiche delle precedenti.
Cataloghi congiunzioni Cinelli anni ’80
È sorprendente quanto potevano essere pessimi gli accessori standard; anche quelli più costosi. Spesso era necessario un importante lavoro di alesatura e limatura, negli angoli e nelle misure corrette, prima di arrivare alla brasatura. I forcellini verticali dovevano essere brasati in modo molto accurato, altrimenti l’allineamento delle ruote era impossibile, quelli migliori erano realizzati in acciaio forgiato o fuso, spesso lavorato per tolleranze esatte, come quelli della Campagnolo.
Cinque classici forcellini posteriori Campagnolo. Sulla destra tre orizzontali usati in molti telai d’acciaio. Corto, medio o lungo; più vecchia è la bicicletta, più lunghi erano solitamente i forcellini.
ACCESSORI SALDOBRASATI
Nell’immagine A, n. 1 parti di brasatura per freni cantilever; n. 2 dall’alto al basso, tre saldature per i bulloni per vite stringi sella; n. 3 /4 ponticelli dei freni; n. 4 due pregiati prodotti Cinelli fusi; n. 3 due tubi semplici, quello curvo si trova solitamente nei telai da pista. N. 5 elementi utilizzati per rafforzare i ponti dei freni. I ponti delle scatole del movimento erano disponibili in diverse dimensioni, potevano essere larghi n.6, piccoli n. 7/8. Nell’immagine 2, n. 1 tre tipi di rinforzi per forcelle anteriori; n. 2 due attacchi a saldare per deragliatole anteriore; n. 3 i passacavi per passare sopra e sotto alla scatola. N. 4 alcuni fermacavi. N. 6 attacchi a saldare al tubo obliquo per manettini del cambio, n. 7 guide passacavi, n. 8 rinforzi per ponti freno o scatole e n. 9 rinforzi per ponticelli. Per saldare i foderi posteriori al telaio si usavano punte a forma di lancia in acciaio n. 10 /11 mentre la costruzione con fogli sciolti n. 12 era più leggera ma più faticosa per il costruttore.
TUBAZIONI
Ovviamente stiamo parlando di tubi in acciaio. I corridori classici del dopoguerra in Europa usavano principalmente bici francesi, italiane e inglesi. Le dimensioni dei tubi e delle filettature nei telai potevano quindi essere diverse. Poco dopo la guerra, le aziende più note erano Reynolds, Falck, Libellula e Mannesman-Dalmine. Negli anni Cinquanta la Cinelli fece produrre alcuni dei suoi tubi alla Columbus e ottenne i diritti per la vendita, diventando un attore importante nel mercato mondiale. Le congiunzioni e le parti a saldare erano fabbriche in Italia principalmente da Cinelli, Roto e Silva in Francia Nervex, Prugnat, Bocama e Vitus. Tutte le aziende hanno usato sistemi metrici e imperiali. Haden, Davis e Reynolds producevano in Inghilterra e, naturalmente quest’ultimo non solo produceva i loro tubi con dimensioni imperiali ma anche in misure metriche per il mercato francese.
La prima colomba del marchio Columbus era su sfondo rosso e il disegno delle ali era molto dettagliato, il testo sotto il disegno era “marca depositata”. Intorno al 1970 la colomba diventò bianca con un disegno meno preciso; il testo venne sostituito dal segno ®. Dopo il 1978 si vede una colomba ad ala singola. Fino alla metà degli anni Ottanta i tubi erano realizzati con acciai al Cromo-Molibdeno; in seguito furono disponibili trovare aggiunte di niobio e vanadio per la saldatura a TIG.
Tubazioni Falk / Catalogo Bozzi 1956
Tubazioni Mannesmann Dalmine / Catalogo Bozzi 1956
Negli anni ’80 il classico tubo tondo fu sfidato da nuove mode e nuovi design, la Columbus creò le tubazioni Aero e il tubo Max insieme a congiunzioni speciali a saldare. Molti telai furono offerti anche in tubazioni oversize per (provare a) competere con carbonio e alluminio aumentando la rigidità del telaio. Nel 2008 (dopo 100 anni!) fu realizzata l’ultima serie Reynolds 531. Gli acciai al manganese erano difficili da saldare e furono stati sostituiti dai tubi al cromo-molibdeno Reynolds 525 e Reynolds 725, che potevano essere saldati e brasati.
I tubi giapponesi di Miyata non sono furono utilizzati dall’industria europea delle biciclette. L’azienda olandese Kowallik & Gaastra era importatrice di biciclette Miyata in Europa (1974). Il know-how di Gaastra (Batavus) e il fatto che le bici siano state costruite secondo le loro specifiche (Koga-Miyata), migliorò la qualità della loro produzione; Myata fece lo stesso per Giant (un fornitore di Schwinn e Specialized all’inizio degli anni ottanta). I tubi di Ishiwata si possono trovare in tutto il mondo, non solo in Giappone, ma anche a Taiwan, negli Stati Uniti e in Europa (Flandria, Jan Janssen, ecc.) L’industria delle biciclette in Estremo Oriente, aveva una fornitura completa di tubi e parti di brasatura, che a volte assomigliavano ai famosi disegni europei. I migliori tubi giapponesi provenivano da Tange e sono stati utilizzati da costruttori europei.
Pagine dal catalogo Reynold del 1920 / Via Kumori
Reynold 531, pubblicità anni ’30 / Via Kumori
Tunbazioni Reynolds
Evoluzione adesivi Columbus / Via cyclesroland
Tubazioni aerodinamiche in acciaio Columbus AIR / Foto from Joe Cosgrove’s Cycle Design by Veloaficionado
Tubazioni Columbus
Tubazioni Columbus nei modelli Mondonico
Tubazioni Columbus Multishape
Top di Gamma tubazioni Tange
Kit tubi Columbus Cromor e piccole parti a saldare Silva